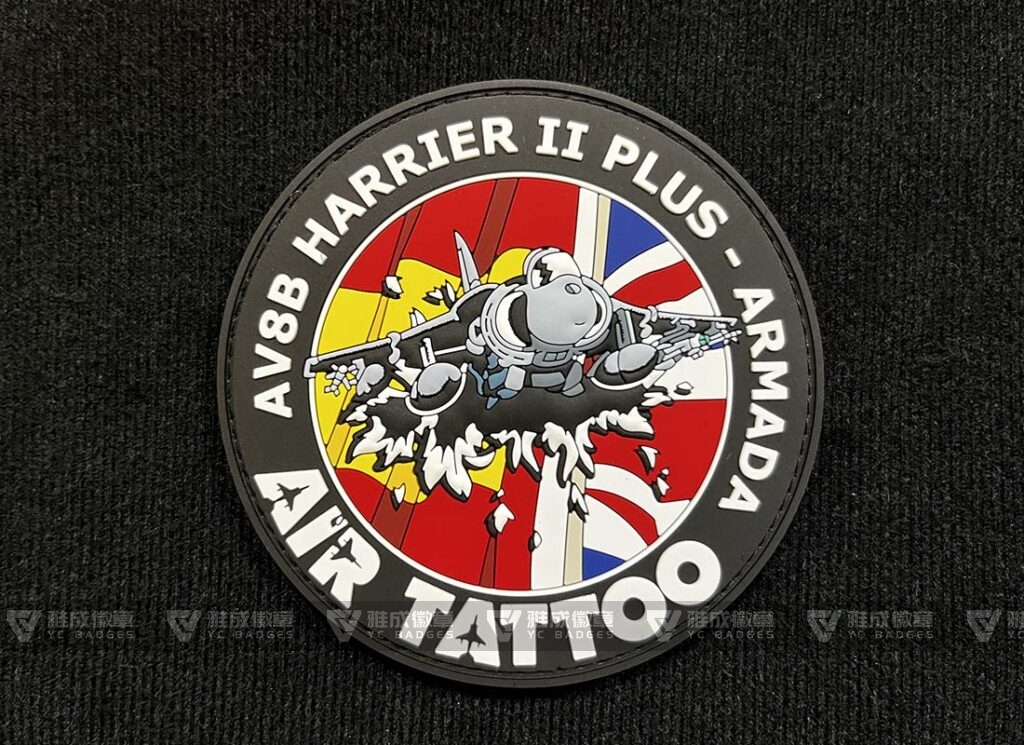
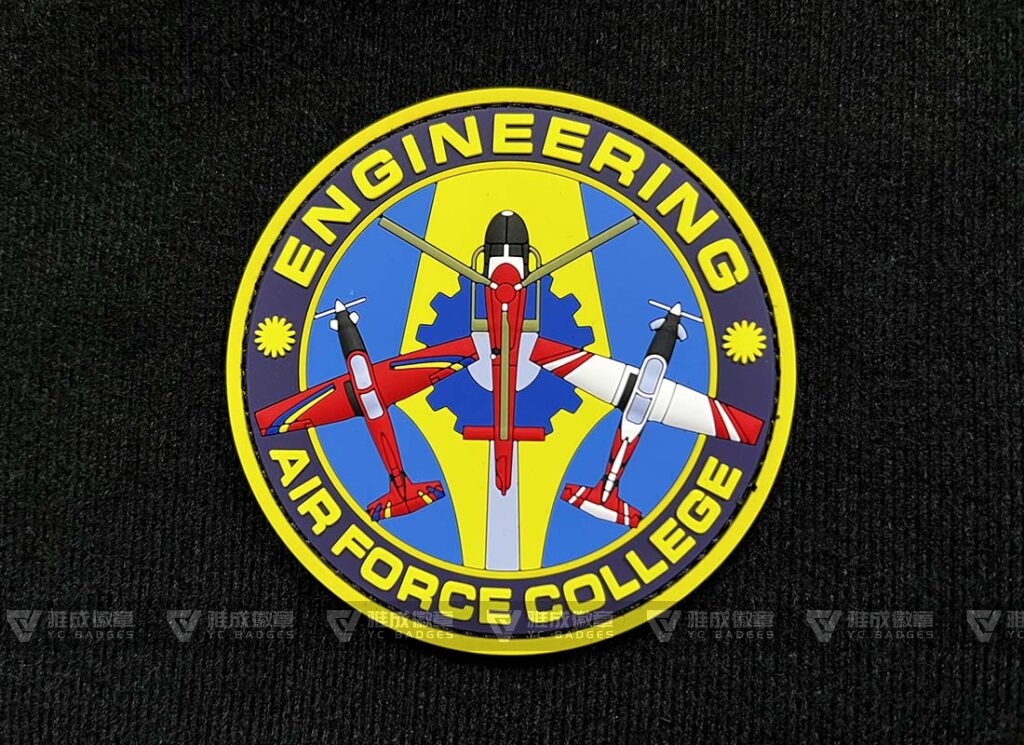
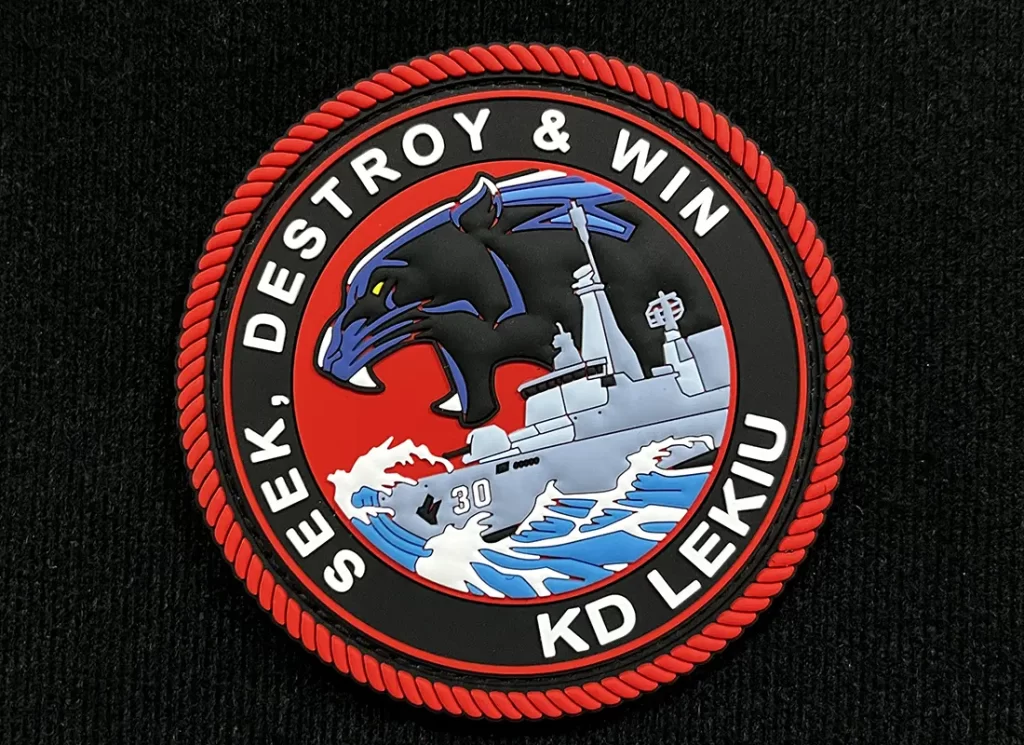
Are there any size limitations for custom PVC patches?
In the world of personalized fashion, branding, and DIY projects, custom PVC patches have become a popular choice. They offer a durable and eye – catching way to express individuality or promote a brand. A question that often arises is whether there are size limitations when it comes to these patches. The answer is a bit more complex than a simple yes or no, as several factors come into play.
1. Manufacturing Constraints
- Production Equipment: The machinery used to create custom PVC patches does impose some practical size limitations. Most manufacturers have standard – sized molds and printing equipment. Smaller production set – ups may be more restricted in the size of patches they can produce. For instance, if a company uses a smaller – scale heat – pressing machine for shaping the PVC, it might have a maximum bed size. This could limit the size of the patch to, say, a few inches in width and length. Larger industrial – grade equipment, on the other hand, can handle more substantial dimensions, sometimes up to a foot or more in length and width.
- Material Thickness and Handling: The thickness of the PVC material also affects the feasible size. Thicker PVC is more rigid, which can make it challenging to create very large patches without additional support or reinforcement. If a patch is too large and the PVC is thick, it may warp or not maintain its shape properly. Additionally, handling large sheets of PVC during the manufacturing process can be cumbersome. Workers need to be able to manipulate the material easily for processes like cutting, printing, and finishing. If the patch size becomes too unwieldy, it can disrupt the production flow and lead to quality issues.
2. Design and Aesthetic Considerations
- Detail Resolution: When it comes to the design on the PVC patch, size can impact the clarity of details. For very small patches, intricate designs may become difficult to discern. For example, if you have a logo with fine lines or a detailed illustration, reducing it to a tiny size might make these elements blend together, losing their visual impact. Conversely, for extremely large patches, maintaining the proportion and balance of the design can be a challenge. A design that looks great on a small patch may appear stretched or out of place when blown up to a much larger size.
- Application Surface: The size of the patch should also be appropriate for the surface it will be applied to. A massive PVC patch might overwhelm a small item like a keychain or a delicate piece of jewelry. On the other hand, a tiny patch may get lost on a large backpack or a denim jacket. The size needs to be in harmony with the host item to enhance its overall aesthetic.
3. Cost – Related Factors
- Material and Production Costs: Larger custom PVC patches require more material, which directly increases the cost. The manufacturing process for larger patches may also be more complex and time – consuming. For instance, printing a large – scale design on a big patch may need more ink and multiple passes of the printing machine, adding to the production cost. This cost factor can act as an implicit size limitation, as customers may be deterred by the high cost of producing very large patches.
- Economies of Scale: In some cases, smaller patches can be produced more cost – effectively in large quantities due to economies of scale. Manufacturers can fit more small patches on a single sheet of PVC during the production process, reducing the per – unit cost. As the patch size increases, the number of patches that can be produced from a single sheet decreases, potentially making larger patches more expensive per piece.
4. Attachment and Durability
- Attachment Methods: The method of attaching the PVC patch can also influence the size. For example, if you plan to sew on the patch, very large patches may be difficult to sew evenly, especially if they are thick. The weight of a large patch can also put more stress on the stitching, increasing the risk of the patch coming loose over time. Heat – sealed patches also face challenges with large sizes, as it may be harder to ensure a uniform and strong bond across a large surface area.
- Durability: Larger patches are more likely to be subject to wear and tear. They may be more prone to bending, folding, or getting caught on objects, which can lead to damage. To maintain durability, larger patches may require additional reinforcement, such as adding a backing material or using stronger adhesives, which can further complicate the production process and increase costs.
In conclusion, while there are no absolute size limitations for custom PVC patches, a combination of manufacturing constraints, design and aesthetic requirements, cost – related factors, and attachment and durability considerations all play a role in determining the practical size range for these patches. By taking these factors into account, both manufacturers and customers can ensure that the custom PVC patches meet their expectations in terms of quality, appearance, and functionality.